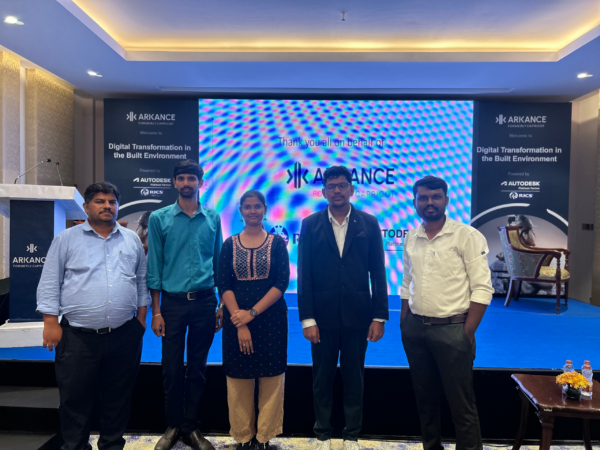
July 15, 2024 | Articles
Construction’s Digital Transformation & The Tools of Modern Project Management
In 2015, Phoenix voters opted to fund a 35-year, $31 billion transit plan encompassing new bus service, light rail capacity, and street improvements spanning approximately 42 miles and connecting the major metro areas of Phoenix, Tempe, Mesa, Chandler, Gilbert, and Tempe. Hill International, Inc. is supporting the Valley Metro Regional Public Transportation Authority (Valley Metro) as Project Manager in delivering this ambitious program, providing program management and construction management services across multiple phases.
Two of the program’s most complex and high-profile projects are currently nearing completion: the Tempe Streetcar project and Valley Metro’s Operations and Maintenance Center Expansion. Each of these projects presented a suite of challenges, from coordination with third parties to minimizing operational impacts. But, through close coordination with all stakeholders and a proactive approach to finding solutions, both projects achieved Valley Metro’s goals and are ready to further connect the Phoenix metro community. “We are grateful for the partnership with Hill International in delivering these important projects to the Valley,” said Valley Metro’s Brain Mason, Manager, Construction and Utilities.
Tempe Streetcar
The $200 million Tempe Streetcar project provides a regional commuting solution for the city of Tempe by connecting a residential area at Apache Boulevard, across from the Arizona State University campus in downtown Tempe, with Rio Salado Parkway at a busy commercial/business center terminus. Streetcar also enables intermodal connection with Valley Metro’s light rail system at Mill Avenue and Apache Boulevard.
This CM-at-Risk project installed a total of 6.3 miles of rail, with 3.8 miles of single and double track segments, 7 single turnouts, and 2 crossovers. As streetcar track is shared with local traffic, the project also necessitated 19 grade crossings in downtown Tempe. In addition, the streetcar has 14 stops, each featuring installation artwork from local artists. An overhead catenary system (OCS) provides power for streetcar, delivered by three traction power substations. These substations are adorned with high-finish architectural wall panels to complement the local urban streetscape. In addition, for a length of track running from Mill Avenue to Tempe Beach Park, streetcar runs on battery power, temporarily eliminating use of the OCS and preserving downtown Tempe’s lush tree canopy.
To help realize the project as planned, the project management team worked in close collaboration with the City of Tempe government and the contractor to solve problems in the field, keep the project on budget, and meet schedule requirements. A highlight of the team’s work was change management support, as $14 million in contract change orders were made over the three-year construction phase of the project. These modifications included Issued for Bid-to-Issue for Construction adjustments, roundabout construction, and the Dorsey power switches, which were designed during construction to upgrade Valley Metro’s light rail system.
The PM team also managed hundreds of conflicts between the OCS with both underground and overhead utilities. Similarly, we helped to identify and resolve conflicts between the Streetcar track slab and the existing road geometry and the local drainage system, which encompassed additional grading and paved areas beyond the original design. Additional power connections between local providers and service entry systems were made during construction as well. In each case, the team discussed design and construction methods, with Hill providing independent cost estimates to provide clarity and increase cost certainly.
Another key area where PM team directly contributed to project success was through design evaluation support. Reviewing designs during construction, we identified modifications such as simplified traffic signals and streetlight connections, unnecessary catch basins, duct bank changes, and even contract allowance adjustments. Our work resulted in a $4 million credit to the project. The team also contributed to Integration Test Coordination for the project, as well as Safety & Security Certification.
The project also identified several lessons learned for Valley Metro to integrate into future projects applicable to other transit agencies delivering their own streetscape projects. These included:
Operations and Maintenance Center Expansion
The $92 million, design-build Operations and Maintenance Center Expansion Project (OMCEXP) delivered yard and shop facilities to accommodate a fleet of 40 additional vehicles along with all associated maintenance and service space requirements, including critical infrastructure upgrades. Now completed, the expansion enables Valley Metro to maintain a fleet of approximately 90 vehicles, compared to the former capacity of 50 vehicles.
The project included adding 35,500 square feet of Maintenance of Equipment (MOE) space and 25,000 square feet of working area to the Maintenance of Way (MOW) building. The yard itself was raised using a mechanically stabilized earth (MSE) wall and engineered fill to add 3 new, 1,500 linear feet of storage tracks, and 5 new service bays were added in the MOE. In addition, work in the yard included 6,600 linear feet of new trackwork, and greater flexibility and movement was delivered by adding 16 new turnouts and adjusting 3 switches to maximize geometry in the yard. Construction of these elements was achieved in an active yard, without disrupting mainline revenue service.
The project also revamped the cooling systems in the MOW and MOE buildings, and especially in the shop spaces for the light rail vehicle (LRV) mechanics. The MOE now cools 174,000 square feet of shop space to 75 degrees Fahrenheit year-round with a fresh air ERV / ARU cooling tower system. The project also added an additional substation to the yard, replaced train wash equipment, improved system safety by installing a new sanding system for the LRVs, and added two new cleaning platforms. Notably, these systems needed to allow for two new dynamic vehicle envelopes: the Siemens LRVs and the Brookville streetcars, as well as accommodate the current Kinkisharyo LRVs for clearance and safety in the shop and yard.
Upgrade and repair elements of the project included correcting the tension of the OCS in the yard, replacing failing components, and bringing the overall facility to a state of good repair, all while maintaining operations for vehicles and staff.
Specifics of the OMCEXP included:
Resident Engineering support was critical on this project, as Valley Metro was able to leverage its current specifications with Hill’s global body of rail program and project best practices and lessons learned. This included specific experience drawn from light rail projects across the U.S. as well as internationally and helped the team to control costs throughout the project lifecycle. Areas where Hill’s expertise directly benefited the OMCEXP included ensuring compliance with specifications, design, and safety concerns during systems integration testing; confirming emergency management plans were in place and updated regularly (this included six separate incidents where the contractor placed equipment within the track’s fouling envelope, scratching a train); and implementing a safety call tree early in the project to keep all project parties informed and up to date.
Another area where PM support was critical was in addressing a significant amount of planning and preparation requirement by Valley Metro. This effort was necessitated due to internal concerns between the Operations and the Planning departments, as Operations asked the project to further minimize impacts to operations than had originally been agreed upon.
All Aboard
With several extensions and studies currently either underway or in planning for Valley Metro, the team is looking forward to delivering additional assignments and leveraging the lessons learned and best practices from the Tempe Streetcar and Operations and Maintenance Center Expansion projects. In addition, the PM team’s growing familiarity with Valley Metro’s internal preferences and procedures means the team will be able to support our assignments with greater and greater efficiency and effectiveness.
Gregory Heinz, Senior Vice President, Western Region Manager
Phone: 425-999-0953
Email: [email protected]
For more about Hill’s rail and transit experience around the world, click here: www.hillintl.com/projects/rail-transit
Share
July 15, 2024 | Articles
Construction’s Digital Transformation & The Tools of Modern Project Management
July 10, 2024 | Articles
GC/CM at Post Falls: Managing Avista’s North Channel Dam Rehabilitation Project
June 23, 2024 | Articles
Irv Richter – An Innovator, A Pioneer, A Leader (1944 – 2024)
June 14, 2024 | Articles
Environment of Care Standards – Meeting the Challenge (Part Two)
June 13, 2024 | Articles
PMO for Public Transit Project Success: The Reopening of Philadelphia’s Franklin Square Station
June 7, 2024 | Articles
May 17, 2024 | Articles
Hill Interim Federal Market Sector Leader Jane Penny Receives Golden Eagle Award
April 11, 2024 | Articles
A Model Move: Managing Move-In at the Sylvia H. Rambo U.S. Courthouse