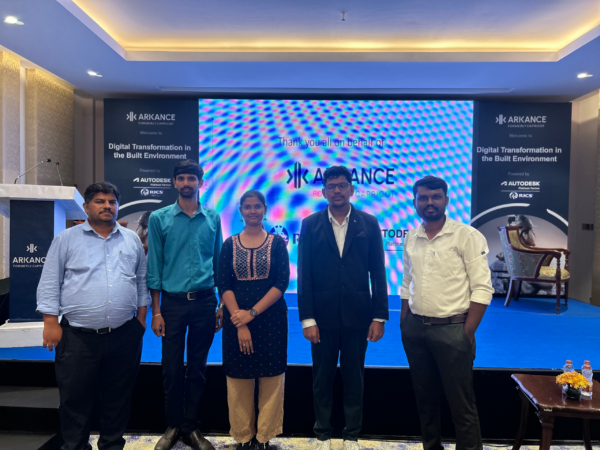
July 15, 2024 | Articles
Construction’s Digital Transformation & The Tools of Modern Project Management
In the first two installations of this safety culture series, we’ve discussed the importance of safety culture, taken a look at how to implement a safety culture with a focus on timing, and explored the role of the safety professional in shaping that culture. While I’ve said over and over that a strong safety culture is the key to successful safety outcomes on construction projects, you shouldn’t just take my word for it. So, in the third part of this series, I’d like to look at the impact of a well implemented safety culture on real projects. Specifically, Hill’s current work throughout the U.S. for an international oil and gas company demonstrates some of the most important factors in a safety culture, illustrates the importance of timing, shows safety professionals in their roles, and, most importantly, offers results.
The Background & Projects
Currently, Corporate Health, Safety, and Environment (HSE) Manager Bill Mueller, Safety Manager Bea Reynolds, and I provide safety audit and on-site safety representative services to the client for multiple projects around the U.S. The work ranges from asphalt replacement to the construction of new gas stations, complete with underground petroleum tank infrastructure, signage, and canopies. I have a long relationship with this client, and they understand my approach to cultivating safety culture, my prioritization of team building and effective communications, and the technique and attitude I bring to my work. Bill and Bea take the exact same approach, so no matter where a project is, the client knows they’ll get the same level of care and professionalism.
Partially because of my relationship with the client and partially because of the way they structure their project organizations, Bill, Bea, and I are involved in their projects from day one. That means building our safety culture is easier for everyone involved. As I said in the first safety culture article, at the beginning of a project my work is pleasant and easy. We have plenty of time to build leading indicators like training and team building, develop relationships, create a communication plan, provide solutions if safety issues arise, and set the standard for safe behavior on site. That means there’s more trust and more safety infrastructure in place from the get-go. Pleasant and easy, indeed!
Moreover, Bill, Bea, and I have tailored our services and made sure we all have the requisite knowledge and experience to meet the client’s needs prior to any projects commencing. For example, while projects range in location, scale, and scope, they all require a strict commitment to meeting American Petroleum Institute (API) safety standards. Many of these industry-specific safety regulations go above Federal Occupational Safety and Health Administration (OSHA) standards. Sometimes, API standards differ from OSHA standards in very slight ways. Regardless, it’s important to our client, Hill, and everyone else involved on a project that we get our safety audits exactly right. When the client first offered Hill a contract, Bill, Bea, and I were able to get together and go through those standards in detail so none of us had any blind spots going into our work.
Attention to Detail
That brings up another important point about safety culture: there needs to be excruciating attention to detail. Bill Mueller’s maxim, “every choice matters,” sums it up well. From the biggest to the smallest issues, safety professionals have to be dedicated to careful observation and documentation of jobsite practices, plus all the paperwork. If you want everyone on a job site to be aware of the risks they have to face during the day, you have to have a precise understanding of every one of the risks that every one of
those professionals is going to face. The mind reels! And in fact, it’s all too easy to drown in that kind of minutiae—to be fair, this is not a career for everyone. That’s where the attitude I discussed in part two of the series comes in. To keep their eye on the ball, safety professionals need a core conviction that life must be protected, and they need enough compassion to understand that every person on a project has someone who counts on them … strong organizational skills also help!
This attention to detail is important for one of our main tasks as safety reps: visiting sites and conducting audits. As a large oil and gas company, our client uses a checklist audit format to standardize their safety audit process. That saves time and promotes consistent quality across their portfolio. However, without attention to detail, the checklist can be subject to “pencil whipping,” where auditors check a box without understanding its significance or substantiating their check with supporting comments. Checklists can leave management in a difficult place because they have to assume the auditor was thorough, when, in some cases, they were not. That can lead to oversights and increased risk over time. On all of our client’s projects, Bill, Bea, and I add commentary to ensure any high-risk behavior or complacency is reported. We also add detail to make sure the client knows when contractor teams go above and beyond to reduce risk—it’s never all bad news.
The Contract & Communications
One key resource on any project is the contract. A former mentor of mine used a single phrase that has helped me find many answers during my career: “Did you read the contract?” This was always a lighthearted jab but has been a mantra of mine ever since. Still, when evaluating project sites, I ask myself “Hmm, did I read the contract?” Every project has some kind of orientation, but orientation is usually just the CliffsNotes version of the contract’s formal safety plan and there can be a lot that isn’t covered or that is missed altogether. For safety professionals at least, that means a deep engagement with the contract documents is necessary.
Since most of the tradespeople on a job are not reading the full safety plan, it can create a “Caught ya!” situation between the safety managers and everyone else on site. That does nothing good for a safety culture. On our projects with this client, Bill, Bea, and I use a preparation-intensive and creative communications approach to avoid that kind of dynamic. For example, in studying API standards, we make particular note of some of the most easily missed or commonly cited safety issues and relay them to site management and craftspeople. When conducting inspections, if I see work being performed outside of the governing API regulations, I don’t call out for a manager to report it. I initiate a conversation about it with the person completing the task. It usually starts like this: “Hey, I’m Betty and I’m going through and auditing for safety today. Did you know (insert regulation that’s being violated)? It’s a commonly missed regulation, so I wanted to make sure you knew.” This has now pivoted the conversation from “Caught ya!” to “Hey, here is some information you may have missed.” Bill, Bea, and I also compile all these conversations, so we all have access to what our colleagues seeing. This makes for a stronger culture across our client’s entire portfolio.
Measuring Success
At this point, the Hill safety team has successfully completed four projects for the client, and two more are underway. Nevertheless, safety success can be hard to measure. Failures in safety can be the most visible things about a project. However, safety success is generally invisible, often getting eclipsed by the project itself. When things are going right, and that trend line starts to continually move down, it’s similar to losing weight. One day your pants are a little looser, and you think to yourself: “Was it cutting
out soda? That extra walk at lunch? Maybe getting more sleep?” Well, it was probably a combination of several actions repeated over time. But make no mistake, if you stop diligently working at it, the weight (or the risk) will return, and it won’t feel good.
That’s the value of safety culture. While safety success can be invisible, it should be a priority of everyone on a project team. A safety culture shaped by professionals with core convictions and compassion, founded upon communications up and down a project organization, and with rigorous attention to detail helps project organizations maintain and compound their small invisible gains over time. That reduces risk. That reduces injuries. That saves lives.
While I chose to discuss Hill’s contract with this client because it’s a safety-specific role, Hill’s consultants help provide for safety on all of our programs and projects around the world. Bill, Bea, and I, plus the rest of Hill’s Safety Department, help Hill’s project management teams bring a safety culture to every project we’re involved in.
We’re passionate about it. If you have any questions about safety, please get in touch with me at [email protected]. I’m happy to discuss how Hill’s safety professionals or project management teams can help your project build up its safety culture and reduce risk.
About the Author
Elizabeth “Betty” Wilson is an experienced health, safety, and environment (HSE) consultant with a history of working in the construction industry. She is skilled in HSE management systems, HSE auditing, emergency management, workplace safety, and safety management systems. During Betty’s time on various projects with some of the world’s leading engineering and construction companies, she has developed a significant understanding of construction processes and support in high-risk environments. She also has experience leading and training a range of construction personnel from craft workers to supervisors and managers in all aspects of HSE. She is skilled at communicating advice and guidance on all construction HSE related matters throughout organizations.
In her role at Hill as regional safety manager, Betty works with colleagues by confirming health and safety requirements are met, and influences others to recognize and embrace their HSE responsibilities. She is responsible for planning and implementing procedures for Integrated Safe Systems of Work, enforcing safety procedures within the work force, and making sure lessons learned from injury and non-injury accidents are effectively implemented.
Share
July 15, 2024 | Articles
Construction’s Digital Transformation & The Tools of Modern Project Management
July 10, 2024 | Articles
GC/CM at Post Falls: Managing Avista’s North Channel Dam Rehabilitation Project
June 23, 2024 | Articles
Irv Richter – An Innovator, A Pioneer, A Leader (1944 – 2024)
June 14, 2024 | Articles
Environment of Care Standards – Meeting the Challenge (Part Two)
June 13, 2024 | Articles
PMO for Public Transit Project Success: The Reopening of Philadelphia’s Franklin Square Station
June 7, 2024 | Articles
May 17, 2024 | Articles
Hill Interim Federal Market Sector Leader Jane Penny Receives Golden Eagle Award
April 11, 2024 | Articles
A Model Move: Managing Move-In at the Sylvia H. Rambo U.S. Courthouse