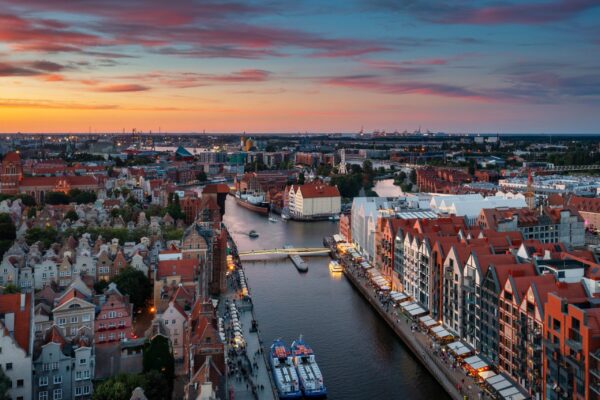
August 27, 2025 | Articles
As an exclusive project and construction management company, Hill International, Inc. (Hill) is often tasked by our clients to manage quality on their programs and projects. This means ensuring that the contractor has processes and procedures in-place to meet the quality requirements of their projects and confirming how these processes and procedures are followed in the field.
Quality control (QC), then, consists of the tasks the contractor undertakes to meet quality requirements, while quality assurance (QA) involves making certain the contractor follows the approved QC plan. Understanding the difference between these two functions can help project teams in several ways, from making sure quality control plans fit the project and the client’s quality expectations to conducting QA/QC activities on site. This is particularly important in today’s construction environment, as the funding from the Infrastructure and Investment in Jobs Act will require recipients from small towns to major transit agencies to adhere to U.S. Federal government standards for quality management on their programs and projects.
QA/QC applies from start to finish on a project, but the cost and schedule benefits are often not apparent until farther along in the project process. The goal should be to drive quality during construction, rather than only emphasizing quality during close out or a phase change. A good rule of thumb is that you can pay a small amount for quality before the project, or you can pay a much greater amount for the same quality after the project is operational. There’s no avoiding the cost in the end—it’s just that addressing quality during construction is a lot cheaper than addressing it after the project is complete.
Understanding the QA/QC process is the first step to implementing the right quality approach for your project.
QA/QC Management
In construction, “quality” generally refers to meeting the expectations of the client for their project. If the project meets the client’s expectations, you’ve delivered a high-quality project. If the project doesn’t, then you’ve delivered a low-quality project. Put QA and QC together and you have a complete quality management system ready to be customized for your project.
Put simply, QC is the process of inspecting construction activities before, during and after they are constructed to confirm the work is being completed per plan and specification. QA is the implementation of proactive processes to improve quality by monitoring and auditing QC activities. AEC organizations from the Project Management Institute to the Construction Management Association of America may differ on the nuances, but these basic definitions apply to almost any project:
Ideally, capturing and disseminating these standards should happen even before the project enters the design phase, as the team can work with the client to develop a Quality Management Plan (QMP—a component of the overall Project Management Plan). Quality control, then, follows as the work done to verify the QMP is adhered to and QA procedures to address any quality shortcomings are already baked in. The QMP also clearly delineates the roles of both the QA and the QC for the project. The goal is to have the QA and the QC work together with a common objective: delivering the best quality project for the client.
Mind Your Qs
The QMP breaks out the quality requirements of the project and then delineates the steps necessary to meet those requirements. In many cases, a key function of the project manager is to develop the QMP as part of their overall PM activities, coordinating with the client, designer, and contractor to make sure nothing is overlooked and that quality control tasks reflect the needs of the project—no more and no less. To use a personal example, if you were having work done on your home, would you simply assume everything was done correctly and as specified, or would you have someone knowledgeable come in to verify the work you paid for is the work you received? The QMP defines what those checks will consist of and how they will be conducted.
On larger projects, the PM team may have dedicated Quality Manager as a stand-alone function. Breaking out this role can be especially helpful on projects of a technical nature, such as transit and rail projects, or any project with a demanding commissioning process, such as a hospital or a public safety building. Notably the Quality Manager does not direct the contractor or get involved in means and methods. Rather the QM can make recommendations on the owner/management level to improve quality control on site.
Reviewing the contractor’s quality plan is a key role of the project management team. This review confirms that there are steps and procedures in place to ensure the final product will meet the client’s requirements—and do so as cost effectively as possible. This can entail code reviews, procurement, and dozens if not hundreds of other line items. During construction the quality plan provides a roadmap of the requirements for testing material used and inspecting the work accomplished for the project. This can be beneficial for projects that use federal, state, or local government funding by producing documented results.
Another key task of the PM’s QA function is to catch any patterns impacting quality. For example, if concrete with a specific mix design consistently fails its strength tests, the QC and the QA should work together to bring that to the attention of the wider team so that the issue is addressed holistically – with, for example, a possible change in the design—rather than piecemeal in the field. The solution reached could not only deal with issues in the moment, but potentially assist with solving long-term warranty issues found later.
To Get What You Expect, You Must Inspect
Once the team delivers the project QMP, quality control begins. QC is boots-on-the-ground aspect of quality management and involves inspecting the techniques, materials, and activities used to fulfill the requirements of the QMP. Note that quality control QC isn’t an effective quality management system on its own because counting on quality to happen based solely on manufacturer specifications and checking work against the contract will result in re-work, lost time, and added cost. Wedding QC to a strong QA function is a much more efficient and effective quality approach.
Examples of quality control on a construction site abound. Materials must be received and verified against the approved project plans, every task and subtask will need to be inspected for completeness and accuracy, and, most importantly, approved safety plans must be followed. This work is fulfilled by the QC on site and confirmed by QA activities.
During construction, QC is responsible for ensuring the contracting team’s work is up to standards. However, when the QC function identifies a quality shortcoming, the quality assurance procedures defined in the QMP dictate how to address those shortcomings. Following the procedures set forth in the QMP establishes the boundaries in which a successful project can be completed. When the QA and the QC are working in harmony, they help deliver a quality project for the owner.
Get What You Pay For
The key to a strong QA/QC approach, as with so many things on a construction project, is communication. A project team with both good formal and informal communications will be able to define and verify quality as efficiently and effectively as possible, all with the goal of delivering the best quality project for the owner.
This supports the goal of QA/QC on any construction project: to deliver the project the client envisions, safely, on time, within budget and with quality. QA/QC supports this outcome in two distinct ways. First, by defining what quality means on the project—from materials to personnel, and second, by executing checks and inspections that confirm the work follows that definition. The result for clients is the peace of mind in knowing the project they paid for is the project they received.
Hill International, Inc. First Vice President C.W. (Bill) Moyers has 33 years of experience in construction engineering, inspection, and project management. He has worked on a variety of transportation, highway, roadway, and bridge projects, including many projects with states Departments of Transportation (DOTs). On his assignments, Bill’s responsibilities include overseeing project timelines, budgets, and safety procedures. He guides teams in project management from the start of a project through completion.
Share
August 27, 2025 | Articles
August 12, 2025 | Articles
Hill Welcomes Ben Schwenk as Senior Vice President in the Kingdom of Saudi Arabia
July 27, 2025 | Articles
The Infrastructure Puzzle: Robert Regalado’s Wholistic Business Development Approach
July 13, 2025 | Articles
Tech-Forward Contracting: A Much-Needed Construction Solution
June 23, 2025 | Articles
Jeffrey Hurley Joins Hill’s Northern California Rail Practice
June 23, 2025 | Articles
Ready, Set, Grow: First VP Chad Koelling Takes Charge of Hill’s Mountain West Region
June 8, 2025 | Articles
PMO in Saudi Arabia: The Holistic Approach to Realizing a National Mega-Portfolio