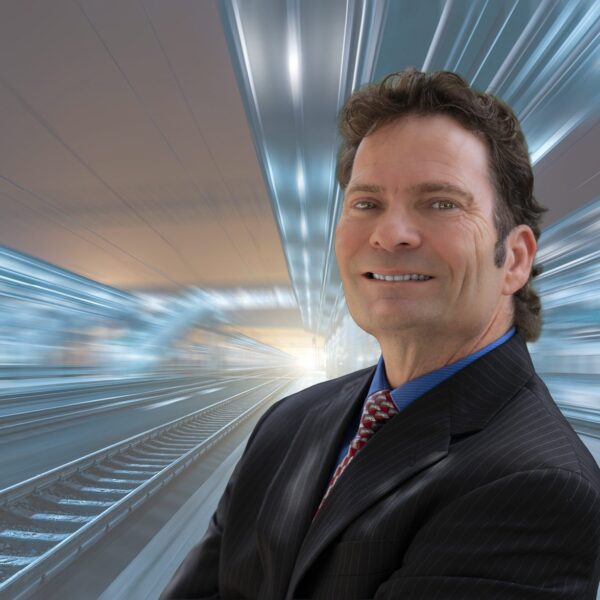
This summer, the Foothill Gold Line Construction Authority and its Program Management Consultant (PMC) Hill International, Inc. handed over the Gold Line Transportation project to Los Angeles County Metropolitan Transportation Authority (Metro). The operations campus serves multiple rail lines for Metro including the Metro Gold Line rail project in California, signifying yet another significant milestone on this important regional transportation project in San Gabriel Valley.
The 24-acre campus, located in Monrovia, was handed over three months ahead of schedule and carried a price tag of about $265 million, said John Skoury, Hill’s Senior Vice President and Program Manager, adding that the campus is a full-service state-of-the-art facility with a capacity to house and maintain up to 84 light rail vehicles and about 200 maintenance and operations staff over several shifts each day. Besides offices and training facilities, the campus also provides a range of maintenance capabilities for light rail vehicles including inspection, heavy repairs, blow-down, wheel truing, body repairs, painting, storage, cleaning and washing. Six miles of track was installed at the facility, much of it located in the storage yard that makes up more than a third of the total site.
For the operations campus, Hill provided construction management services in excess of 500,000 work hours, spent in design and construction over the last four years, Skoury said. “The Foothill Gold Line Operations Campus is one of the only of its kind to be designed and built to meet U.S. Green Building Council’s Leadership in Energy & Environmental Design (LEED) Gold standards,” said Chris Burner, the Chief Project Officer of the Foothill Gold Line Construction Authority. To achieve this, this project employed sustainable components such as smart irrigation systems, LED (light-emitting diode) lighting, recycled and recyclable building materials, solar-powered controllers, and a comprehensive construction waste mitigation program. The main shop building was designed to achieve 35% more water efficiency and 32.5% more optimized energy performance than a typical building of its kind. In addition, a 178.5-kilowatt solar panel array, a large-scale stormwater collection and filtration system and other water and energy conservation features were also built into the facility. With an eye on water savings, innovative features were designed into the campus. The 9,000-square-foot car wash facility, which utilizes an average 60,000 gallons of water each day, was built to use only recycled, reclaimed water.
Challenges and innovations
Like any other project, the operations campus also had issues to be dealt with, Skoury said, citing the case of delays in relocation of businesses on the property where the facility was to be built. “While the contract stipulated properties would be available for demolition by a certain date, negotiations for their procurement and vacancy varied, threatening the schedule,” he said, noting as part of providing a solution the Hill team negotiated early access to several properties, allowing demolition to begin. Insufficient water supply was another hurdle that had to be crossed. “During the final stages of fire water supply design, the design builder determined the maximum GPM available from the city system was 3,700 GPM; far below the mandated delivery of 7,200 GPM. To deliver the additional capacity, the project required a water reserve system. Even though the site plan had already been designed, the Hill team located the 606,000-gallon storage tank and 3,500-GPM diesel pump, with only minor revisions to the site design,” he said.
Innovation was high on Hill’s agenda for project execution. The Hill team worked with its client and the design-builder to identify opportunities to enhance the project and meet challenges creatively, Skoury said. They included acquisition of businesses/parcels for which Hill negotiated early turn-over to the contractor on several acquired businesses, enabling early demolition on most parcels. This mitigated delays in preparing the site for grading among other construction operations. Also on the list was handling any hazmat on site and related mitigation. The CM team mitigated the risk of delays due to discoveries by implementing “immediate response” protocols.
Hill’s contributions to the operations campus on the Gold Line will go down as a major success story for company in which several project components were brought together and the critical path set by the design builder was adhered to strictly. “We applied the best practices of other successful design-build assignments to manage the project, overseeing the Foothill Transit Constructors and working closely with the Authority staff, Metro and the city. The project team also developed a comprehensive risk management program, including quarterly review and mitigation of all risk items, which helped to control costs on the project,” Skoury said.
By Ashok Dutta
Share
June 23, 2025 | Articles
Jeffrey Hurley Joins Hill’s Northern California Rail Practice
June 23, 2025 | Articles
Ready, Set, Grow: First VP Chad Koelling Takes Charge of Hill’s Mountain West Region
June 8, 2025 | Articles
PMO in Saudi Arabia: The Holistic Approach to Realizing a National Mega-Portfolio
June 1, 2025 | Articles
May 26, 2025 | Articles
May 12, 2025 | Articles
Keeping Your Water/Wastewater Programs Flowing with Public Relations
April 27, 2025 | Articles
Oiling the Machine: Steps to Successful Permitting on Infrastructure Megaprojects
April 20, 2025 | Articles
Sustainable Scaling: Solutions for Managing Risk on Europe’s Data Center Projects